The necessary factors to consider in the injection molding process are worthy of collection!
Heat-sensitive plastics and easily hydrolyzed plastics
1. Thermal sensitivity means that some plastics are more sensitive to heat, and the heating time is long at high temperature or the cross-section of the feed inlet is too small, and when the shearing action is large, the material temperature increases and is prone to discoloration, degradation, and decomposition. Plastics with special properties are called heat-sensitive plastics.
Such as rigid PVC, polyvinylidene chloride, vinyl acetate copolymer, POM, polychlorotrifluoroethylene, etc. When heat-sensitive plastics are decomposed, by-products such as monomers, gases, and solids are produced. In particular, some decomposed gases are irritating, corrosive or toxic to the human body, equipment, and molds.
Therefore, attention should be paid to mold design, selection of injection molding machines and molding. Screw injection molding machines should be selected. The cross-section of the gating system should be large. The mold and barrel should be chrome-plated, and there should be no corners. Add stabilizer to weaken its heat-sensitive properties.
2. Even if some plastics (such as PC) contain a small amount of water, they will decompose under high temperature and high pressure. This property is called easy hydrolysis, which must be heated and dried in advance.
5. Stress cracking and melt fracture
1. Some plastics are sensitive to stress, and are prone to internal stress during molding and are brittle and easy to crack. Plastic parts will crack under the action of external force or solvent.
To this end, in addition to adding additives to the raw materials to improve the crack resistance, attention should be paid to drying the raw materials, and the molding conditions should be reasonably selected to reduce internal stress and increase crack resistance. A reasonable shape of plastic parts should be selected, and measures such as inserts should not be set to minimize stress concentration.
When designing the mold, the demolding slope should be increased, and a reasonable feeding port and ejector mechanism should be selected. During molding, the material temperature, mold temperature, injection pressure and cooling time should be properly adjusted, and try to avoid demoulding when the plastic parts are too cold and brittle. , After molding, the plastic parts should also be post-treated to improve crack resistance, eliminate internal stress and prohibit contact with solvents.
2. When the polymer melt with a certain melt flow rate passes through the nozzle hole at a constant temperature and its flow rate exceeds a certain value, obvious transverse cracks on the melt surface are called melt fracture, which damages the appearance and physical properties of the plastic parts.
Therefore, when choosing a polymer with a high melt flow rate, the cross-section of the nozzle, runner, and feed port should be increased, the injection speed should be reduced, and the material temperature should be increased.
Main Features:
One.The Lock Section
1.Arch template, effectively protects the mould, especially suitable for big template with small mold.
2.The electric ruler is installed on the crosshead, the position is more precise.
3.The front connecting rod uses connected structure, increases the rod strength, and easy for assembly
4.The connected tail-board stills itself with big lock shaft, improves tail-board strength, and ensures zero abrasion of the tail-board, easy for maintenance.
5.Connected movable plate, improves its rigidity and reduces deformation
6.Connected thrust bearing, improves its strength and stills itself with small lock shaft, ensures zero abrasion.
7.Arch template fully complies with mechanical property, largely improves template strength.
8.More reasonable toggle design, speeds and stabilizes mold opening and closing.
9.Adjustable movable plate mounting plate, makes the installation easier.
10.Mixed design of T-shape groove and die hole, increases universality of the mold.
Two.The Injection Section.
1.Bridge type support, improves injection smoothness.
2.Longer length-diameter ratio screw design, improves plasticizing effect.
3.Double seal structure, ensures no oil leakage.
4.Withhold type press plate, easy for debugging and assembly.
5.Bijection structure, improves stability.
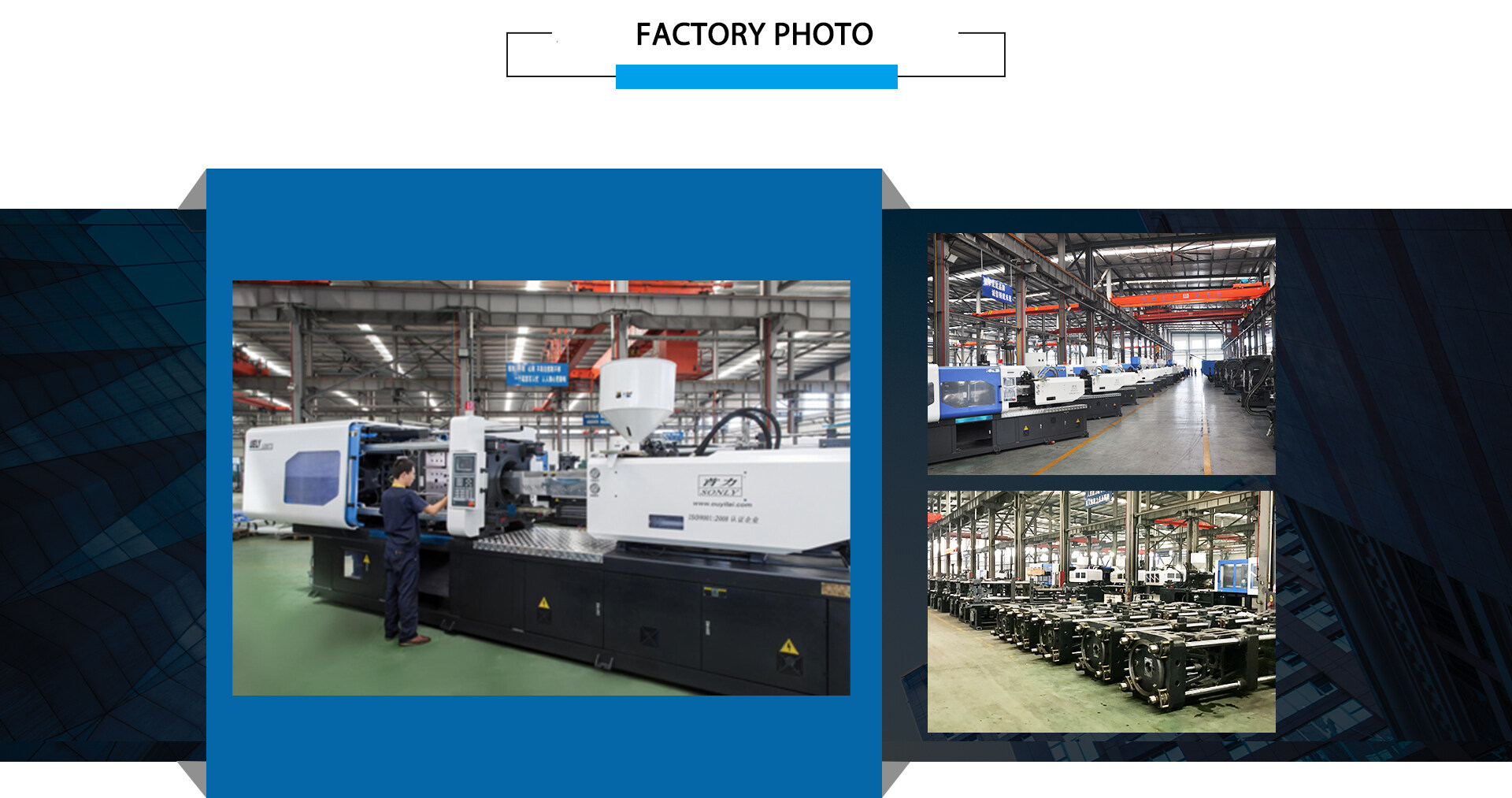
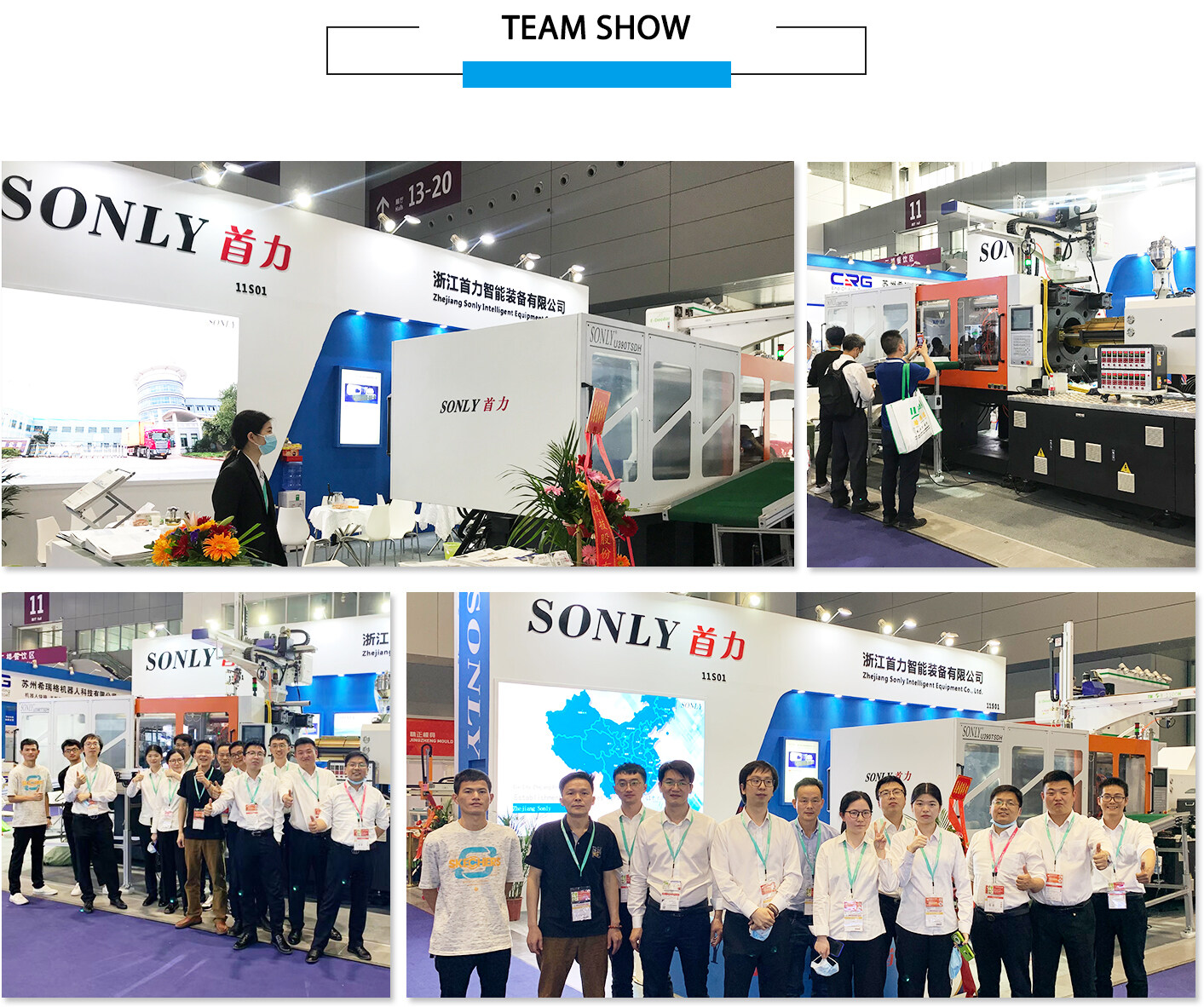
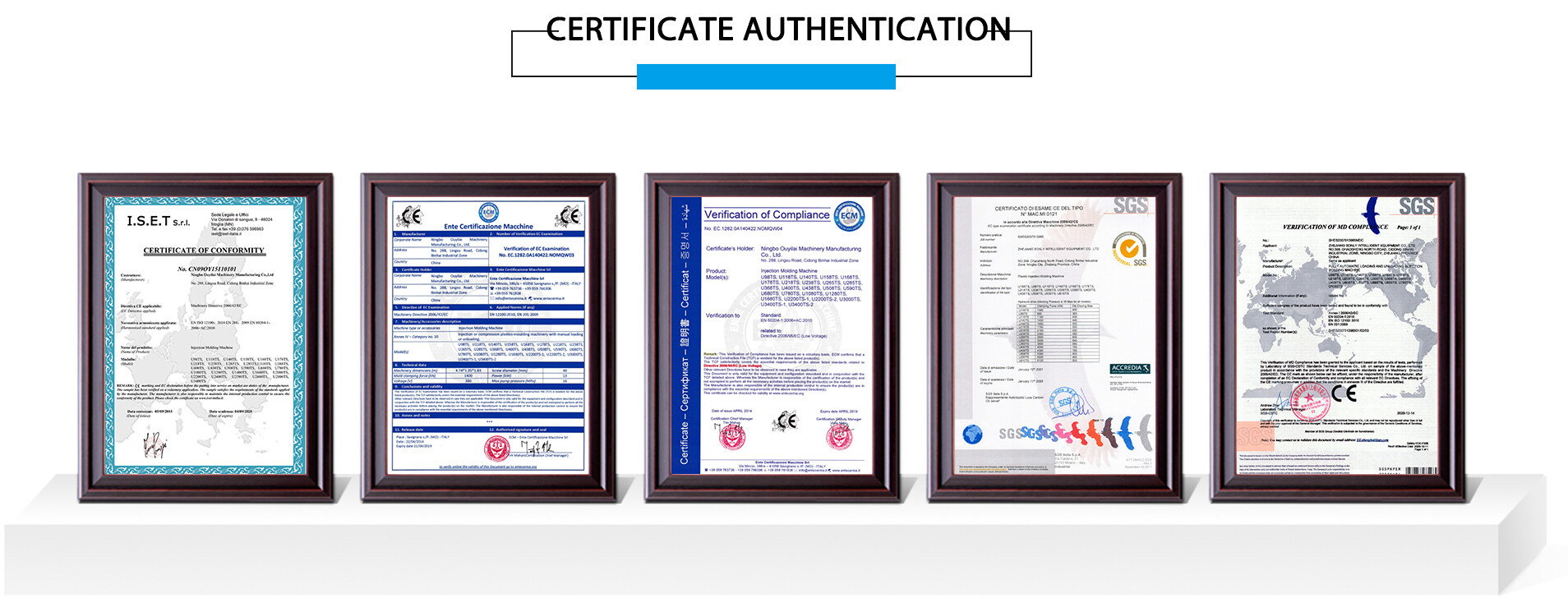
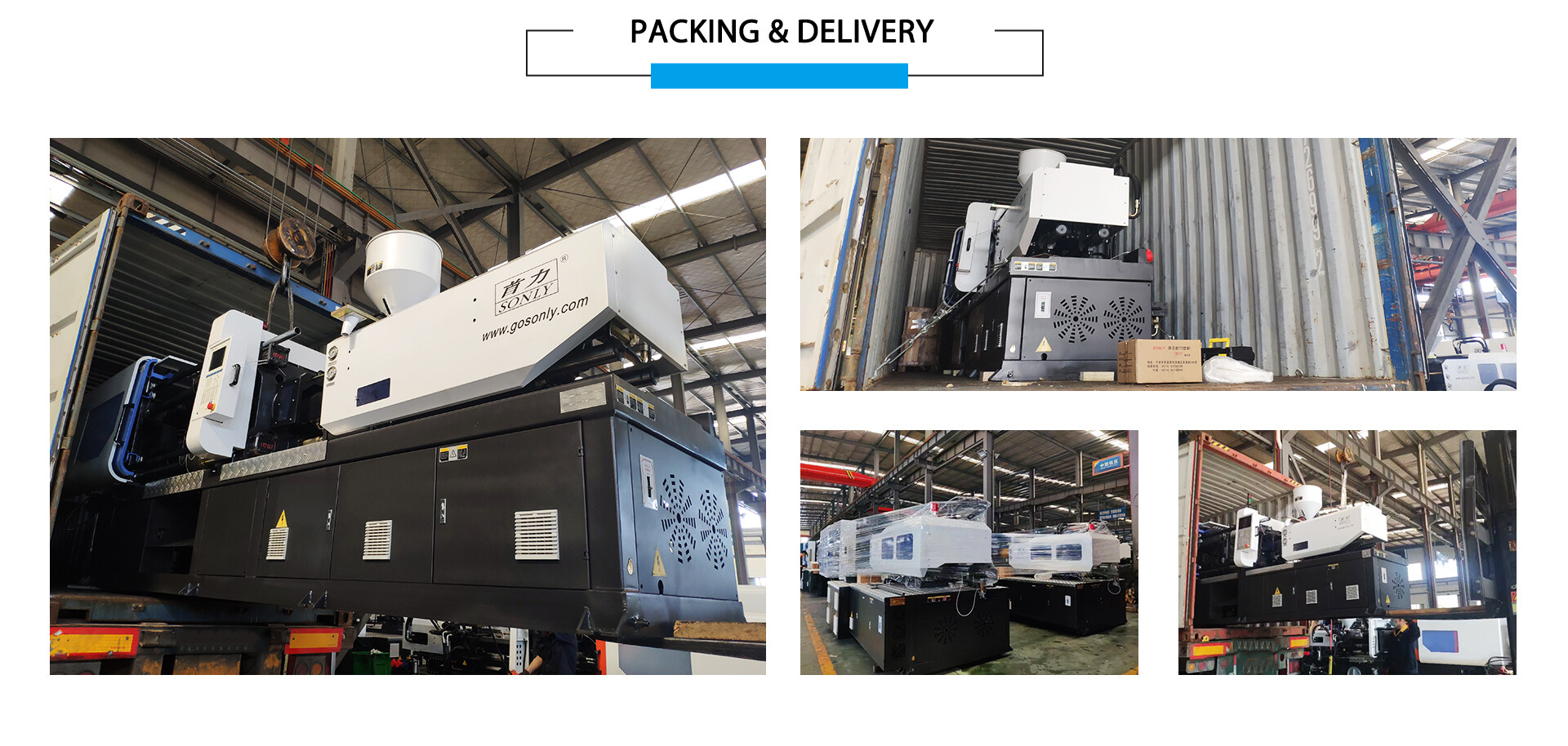